超高強(qiáng)度鋼表面涂(鍍)層防護(hù)處理的研究進(jìn)展
超高強(qiáng)度鋼兼具有高強(qiáng)度(抗拉強(qiáng)度> 1380 MPa、屈服強(qiáng)度> 1200 MPa)及良好的韌性,一般作為重要的承力部件廣泛應(yīng)用于航空航天、艦船、汽車、模具等行業(yè),其典型應(yīng)用包括飛機(jī)起落架、主梁、傳動(dòng)零件、承力螺栓等。常見的超高強(qiáng)度鋼力學(xué)性能如表1所示。該類材料的強(qiáng)度遠(yuǎn)高于常規(guī)材料,部分牌號(hào)抗拉強(qiáng)度已達(dá)到2000 MPa,一般具有相對(duì)較高的氫脆、應(yīng)力腐蝕敏感性。由超高強(qiáng)度鋼制備的零部件,其服役環(huán)境往往十分苛刻,尤其是當(dāng)裝備服役于海洋環(huán)境時(shí),若不采取合理的表面防護(hù)處理工藝,則易在服役壽命內(nèi)發(fā)生氫脆斷裂、腐蝕、應(yīng)力腐蝕、疲勞斷裂、磨損等失效情況,嚴(yán)重時(shí)將導(dǎo)致事故的發(fā)生。例如2002年美國(guó)F14艦載機(jī)起落架減震支柱外筒發(fā)生點(diǎn)蝕,導(dǎo)致機(jī)毀人亡。在超高強(qiáng)度鋼表面制備一層有別于基體組織(成分)的防護(hù)層,是提升超高強(qiáng)度鋼性能,尤其是耐腐蝕、耐磨性能的有效手段?,F(xiàn)階段廣泛使用的防護(hù)工藝包括電鍍與噴涂,涂層或鍍層將基體與外界環(huán)境隔絕開來,顯著提高了超高強(qiáng)度鋼表面的耐腐蝕、耐氫脆、耐磨損等能力,增加了該類型材料零部件的服役壽命。本文綜述了現(xiàn)階段超高強(qiáng)度鋼表面電鍍與噴涂處理的相關(guān)研究進(jìn)展,以期對(duì)相關(guān)領(lǐng)域的工程技術(shù)人員提供技術(shù)指導(dǎo)和理論支持,并對(duì)超高強(qiáng)度鋼表面防護(hù)處理的未來發(fā)展提出了展望。
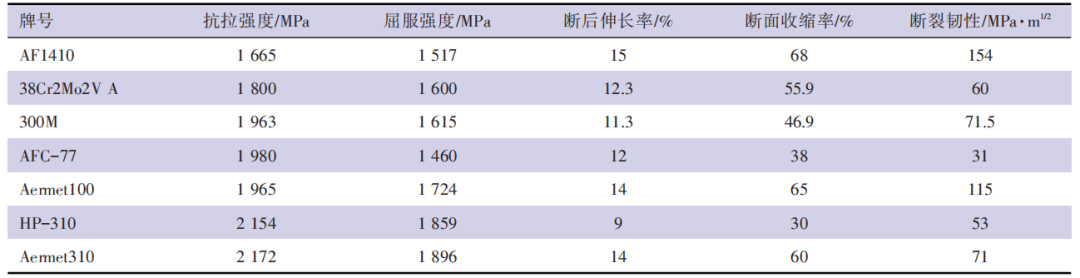
表 1 典型超高強(qiáng)度鋼的力學(xué)性能
一、電鍍
電鍍屬于傳統(tǒng)表面防護(hù)工藝,起源于19世紀(jì)初,意大利科學(xué)家Brugnatelli最早實(shí)現(xiàn)了在銀質(zhì)金屬表面電鍍金工藝。該工藝原理為帶正電的金屬離子M+在陰極沉積,并獲得電子,形成M金屬鍍層。適用于超高強(qiáng)度鋼的主流電鍍工藝具體包括電鍍鉻、電鍍鎘。
1.1 電鍍鉻
電鍍鉻處理可增強(qiáng)超高強(qiáng)度鋼零部件的耐磨和耐腐蝕性能。但目前面臨問題包括:(1)常用的六價(jià)鉻鍍鉻工藝產(chǎn)生酸霧和廢水,污染環(huán)境,其對(duì)動(dòng)植物均有毒性;(2)電鍍鉻工藝通常會(huì)降低基體的疲勞性能,一方面鍍鉻層往往存在內(nèi)裂紋,易出現(xiàn)鍍層磨損、剝落,若鍍層內(nèi)裂紋的密度較高,會(huì)降低試樣的疲勞強(qiáng)度;另一方面,電鍍過程中,陰極會(huì)發(fā)生析氫反應(yīng),增加了材料的氫脆斷裂風(fēng)險(xiǎn),材料的疲勞強(qiáng)度也會(huì)隨之降低。
為降低鍍鉻過程的污染,較為環(huán)保的三價(jià)鍍鉻工藝受到了較多學(xué)者青睞。Gruba等指出通過優(yōu)化電解液成分,采用新的電解液成分(基于三價(jià)鉻離子的四鉻酸鹽電解液等),引入添加劑(氧化鎂、鎢酸鈉氟化銨等),可優(yōu)化鍍鉻工藝。部分學(xué)者在對(duì)電解液成分改進(jìn)的同時(shí),還引入了細(xì)小硬質(zhì)相顆粒,進(jìn)一步增強(qiáng)鍍鉻層性能。
Khani等通過三價(jià)鉻浴法在超高強(qiáng)度鋼AISI 4140基體上電沉積了復(fù)合鉻涂層,通過在電解液溶劑中加入聚溴化十六烷基三甲銨、二烯丙基二甲基氯化銨和氧化鋁粒子,提高離子傳輸性質(zhì),獲得了一種均勻的復(fù)合鉻鍍層,其維氏顯微硬度達(dá)到860 HV,厚度為42 μm,性能與傳統(tǒng)鉻酸電解液所得的鍍鉻層相當(dāng)。隨氧化鋁粒子的加入,涂層中裂紋寬度由3 μm降低至200 nm,氧化鋁顆粒與金屬共沉積狀態(tài)下,將阻斷金屬晶粒生長(zhǎng),并提供更多的形核質(zhì)點(diǎn),降低應(yīng)力水平,且氧化鋁顆粒本身硬度較高,形成復(fù)合鍍層后增加了鍍層硬度與耐磨性能。
Liao等在含納米氮化硅懸浮的三價(jià)鍍鉻液中,在直流條件下電沉積得到了Cr-C/Si3N4復(fù)合鍍層,隨著電鍍槽中Si3N4濃度、電流密度的上升,制備鍍層中Si3N4粒子體積分?jǐn)?shù)均先升高后下降,僅在電鍍槽中Si3N4濃度為5 g/L,電流密度為20 A/dm2時(shí),氮化硅均勻分布在電沉積的Cr-C基體中,體積分?jǐn)?shù)達(dá)到17.22 %,鍍層顯微硬度達(dá)到950 HV,并獲得較好的耐磨性能。
為提高鍍鉻材料的疲勞性能,必須控制鍍鉻層中的微裂紋擴(kuò)展或調(diào)控殘余應(yīng)力,較為有效的方法為包括制備多層復(fù)合鍍層或噴丸強(qiáng)化。多層復(fù)合鍍(涂)層比單一鍍(涂)層性能更加優(yōu)異,尤其是抗裂紋擴(kuò)展的能力,當(dāng)裂紋要通過鍍層界面時(shí),界面兩側(cè)材料性能的差異使裂紋易于偏轉(zhuǎn)和分叉,并降低了裂紋尖端的應(yīng)力強(qiáng)度因子。
Voorwald等研究了在超高強(qiáng)度鋼AISI 4340基體上化學(xué)鍍鎳-電鍍鉻復(fù)合鍍層試樣的旋轉(zhuǎn)彎曲疲勞性能,相較于單一鍍鉻層試樣,試樣疲勞性能有較大提高,復(fù)合鍍層試樣疲勞性能與無鍍層的AISI 4340試樣相當(dāng),鍍鎳中間層的存在能夠抑制硬鉻外層許多原始裂紋的擴(kuò)展,從而顯著提高試樣的疲勞性能。在電鍍之前,對(duì)零件進(jìn)行噴丸處理,可在表面形成壓應(yīng)力區(qū)域,將有效抑制電鍍層裂紋向基體的傳播。Nascimento等先在超高強(qiáng)度鋼AISI 4340基體進(jìn)行了噴丸處理,再進(jìn)行電鍍硬鉻處理后,其疲勞強(qiáng)度高于未噴丸處理的試樣。
Sundar等研究了在超高強(qiáng)度不銹鋼15-5 PH基體表面進(jìn)行激光噴丸預(yù)處理+電鍍硬鉻處理后試樣的三點(diǎn)彎曲疲勞性能,其疲勞壽命高出單一電鍍硬鉻試樣47%,在鍍層與基體界面處,可觀察到裂紋擴(kuò)展路徑的偏轉(zhuǎn)及疲勞條帶的形成,疲勞裂紋萌生自鍍層處的微裂紋,在殘余壓應(yīng)力的基體區(qū)域發(fā)生多次偏轉(zhuǎn),延緩了疲勞裂紋的擴(kuò)展,從而增加了試樣的疲勞壽命。電鍍鉻防護(hù)處理工藝已有百年歷史,現(xiàn)在廣泛應(yīng)用于有耐磨需求的超高強(qiáng)度鋼零部件中,在不斷改進(jìn)工藝的同時(shí),也朝著納米強(qiáng)化、復(fù)合鍍層、壓應(yīng)力控制等方向持續(xù)發(fā)展,從而使鍍層防護(hù)性能不斷增加。
1.2 電鍍鎘及相關(guān)電鍍工藝
耐磨性要求較低的超高強(qiáng)度鋼零部件,其表面通常采用電鍍鎘進(jìn)行防護(hù),增加耐腐蝕性能。鎘的標(biāo)準(zhǔn)電極電位(-0.40 V)稍高于鐵(-0.44 V),但是在海洋性大氣、海水、氯化物的環(huán)境中,其電位將低于鐵,易于形成一層堿式碳酸鹽保護(hù)膜。
鎘鍍層優(yōu)勢(shì)在于:通常作為陽極性保護(hù)鍍層,即使鍍鎘層發(fā)生受到損傷使基體材料裸露,依然可以起到良好的防護(hù)性作用,且對(duì)超高強(qiáng)度鋼與鋁、鎂合金的接觸腐蝕也有很好的抑制作用。鍍鎘層還具有高潤(rùn)滑性,只需施加適中的力矩就能產(chǎn)生所屬的螺栓負(fù)載,因此在超高強(qiáng)度鋼緊固件中也有較多應(yīng)用。與鍍鉻類似,鍍鎘過程中,陰極鎘在沉積的同時(shí)氫離子還原為氫原子,易穿過鍍層進(jìn)入基體導(dǎo)致氫脆的發(fā)生。鑒于超高強(qiáng)度鋼的氫脆敏感性較高,實(shí)際使用的電鍍鎘工藝包括松孔鍍鎘、電鍍鎘鈦、刷鍍鉻等工藝,這些工藝的共同特點(diǎn)為低氫脆特性。
目前關(guān)于鍍鎘防護(hù)的超高強(qiáng)度鋼的研究熱點(diǎn)有兩個(gè):一個(gè)是氫相關(guān)研究,電鍍過程引入氫導(dǎo)致氫脆失效一直都備受研究者關(guān)注。湯智慧等對(duì)比研究了高強(qiáng)度鋼30CrMnSiNi2A和40CrNi2Si2MoVA表面松孔鍍鉻、電鍍鎘鈦、氯化銨鍍鎘和光亮氰化鍍鎘制備鍍層對(duì)基體氫脆的防護(hù)特性,除光亮氰化鍍鎘工藝外,其余工藝下基體氫含量均較低,但實(shí)際生產(chǎn)過程中氯化銨鍍鎘過程可能會(huì)由其他原因?qū)е職錆B入,而該工藝電鍍后鍍層較為致密,烘烤處理氫不容易溢出,實(shí)際工程化應(yīng)用應(yīng)該相對(duì)保守,所以可認(rèn)為松孔鍍鉻與電鍍鎘鈦鍍層的氫脆防護(hù)性能較好。
Reddy等研究發(fā)現(xiàn)鍍鎘的18Ni250超高強(qiáng)度鋼螺栓經(jīng)185 ℃保溫6 h的烘烤熱處理除氫不完全,且螺紋切削加工導(dǎo)致應(yīng)力集中,綜合作用使螺栓僅服役11500 h即發(fā)生氫致延遲斷裂,因此對(duì)于需鍍鎘防護(hù)的超高強(qiáng)度鋼螺栓,建議除氫熱處理的時(shí)間延長(zhǎng)至23 h,以盡可能去除基體中的氫,且應(yīng)采用螺紋滾壓加工代替切削加工降低應(yīng)力集中,從而提高螺栓服役壽命。
Bellemare等采用熱脫附譜儀和持久拉伸試驗(yàn)研究了AISI 4340鋼表面鍍鎘層致密度對(duì)氫脆的影響,通過改變電流密度并僅對(duì)部分試樣噴砂處理,制備了不同密度鍍層的試樣,高密度鍍層的試樣中鍍層孔洞較少,烘烤處理過程氫溢出困難,在190 ℃下烘烤23 h不能去除氫脆,持久拉伸試驗(yàn)未達(dá)到預(yù)定的200 h即發(fā)生失效,需提高烘烤溫度至220 ℃以消除氫脆。該團(tuán)隊(duì)還研究了鍍鎘AISI 4340鋼缺口棒材試樣的氫分布和烘烤延遲對(duì)氫脆的影響,鎘涂層中的氫質(zhì)量濃度較高,可達(dá)到200~1500×10-6(原子分?jǐn)?shù)比),但鍍層與基體中MnS氫陷阱中的氫均不會(huì)對(duì)氫脆產(chǎn)生影響,真實(shí)臨界氫質(zhì)量濃度閾值較低,僅為0.6×10-6(原子分?jǐn)?shù)),且并沒有發(fā)現(xiàn)烘烤延遲對(duì)氫脆的影響。
另一個(gè)熱點(diǎn)是替代鍍鎘的相關(guān)電鍍工藝研究。鎘及其化合物具有較高的毒性,電鍍鎘產(chǎn)生的廢水最終會(huì)進(jìn)入土壤,污染土壤和地表水,并易于在人體中累積會(huì)導(dǎo)致急性和慢性中毒。各國(guó)普遍對(duì)電鍍鎘進(jìn)行限制,并積極尋找相應(yīng)的替代工藝,歐洲法律明確規(guī)定一般工程用途不再允許使用鍍鎘,美國(guó)和日本在內(nèi)的許多其他國(guó)家對(duì)鎘的使用也存在嚴(yán)格的限制,電鍍鋅鎳、鋅鈷等替代工藝受到廣泛關(guān)注。
Sabelkin等對(duì)比研究了表面電鍍鎘與電鍍鋅鎳的AISI 4340鋼試樣的鹽水環(huán)境下的拉壓疲勞性能,兩種鍍層試樣的腐蝕疲勞壽命接近,且鍍層表面有劃痕損傷的試樣與未損傷的試樣相比,未見明顯差異,兩種鍍層在損傷狀態(tài)下依然起到了防護(hù)作用。
Hillier等研究了AISI 4340鋼基體上分別電鍍鋅-1%鈷、電鍍鋅-10%鎳與電鍍鎘試樣的氫脆性能,通過慢拉伸試驗(yàn)測(cè)定了電鍍過程吸收氫對(duì)鋼力學(xué)性能損失的影響以及鍍后烘烤處理對(duì)鋼力學(xué)性能恢復(fù)的效果。電鍍鋅-1%鈷烘烤處理后,機(jī)械性能并未完全恢復(fù),有較大的脆化失效風(fēng)險(xiǎn),但在電鍍鋅-1%鈷涂層前先沉積0.5 μm鈷中間層,再烘烤后幾乎完全恢復(fù)了機(jī)械性能。鈷層作為氫的充分屏障,在烘烤處理期間,涂層中的氫逃逸到大氣中,而不是擴(kuò)散到鋼中。電鍍鋅-10%鎳引起的氫脆最少,這是由于在涂層/基底界面上先形成了富鎳層,而鎳具有非常低的氫擴(kuò)散系數(shù)。
綜合考慮超高強(qiáng)鋼表面的防護(hù)層的阻隔防護(hù)性能、犧牲防護(hù)性能,海洋大氣防護(hù)性能、與鋁合金的兼容性、摩擦性能、疲勞性能、氫脆性能和可修復(fù)性,電鍍鎘工藝表現(xiàn)出優(yōu)異的綜合特性,目前仍然廣泛應(yīng)用于超高強(qiáng)度的鋼防護(hù)處理,尚未有一種工藝能完全替代鍍鎘工藝。但是考慮到鎘及電鍍過程中使用的氰化物的毒性,發(fā)展綠色環(huán)保的新型防護(hù)層技術(shù)是未來的一個(gè)主要發(fā)展方向。
二、噴涂
噴涂工藝最早誕生于1910年,瑞士Schoop博士受兒童鉛丸玩具槍啟發(fā),發(fā)明了第一個(gè)金屬噴射裝置,并命名為金屬噴鍍。對(duì)于超高強(qiáng)度鋼而言,主流的噴涂工藝包括高速火焰噴涂與冷噴涂。
2.1 高速火焰噴涂
高速火焰噴涂通過燃燒劑與助燃?xì)怏w燃燒產(chǎn)生高壓并經(jīng)過膨脹噴嘴產(chǎn)生高速焰流,噴涂粉末被高速焰流中加熱加速,噴射到基體表面形成涂層。現(xiàn)階段高速火焰噴涂工藝主要包括高速氧燃料火焰噴涂工藝(HVOF,High Velocity Oxygen Fuel))與高速空氣燃料火焰噴涂工藝(HVAF,High Velocity Air Fuel)。
有關(guān)超高強(qiáng)鋼表面高速火焰噴涂涂層防護(hù)處理的相關(guān)研究,集中于兩方面,一是高速火焰噴涂涂層與電鍍鉻鍍層防護(hù)性能的對(duì)比研究。Nascimento等分別制備了以AISI4340鋼為基體的硬鉻鍍層試樣與WC-12Co涂層試樣,進(jìn)行了軸向疲勞、旋彎疲勞、耐鹽霧腐蝕與摩擦磨損性能測(cè)試。WC-12Co涂層的耐磨性更好,磨損量更小,且其耐鹽霧腐蝕性能高于常規(guī)電鍍?cè)嚇印?
宋進(jìn)兵等研究發(fā)現(xiàn)A100鋼為基體的WC-CoCr涂層試樣與電鍍硬鉻試樣相比,具有更好的耐磨與耐腐蝕性能。代雪婷等對(duì)比研究了AF1410超高強(qiáng)度鋼表面WC-10Co-4Cr涂層和硬鉻鍍層的耐磨與電化學(xué)性能。兩者的耐蝕性能接近,但WC-10Co-4Cr涂層耐磨性能更為優(yōu)異,具有更小的摩擦系數(shù)與低的磨損量。以上研究結(jié)果均表明,高速火焰噴涂涂層防護(hù)性能優(yōu)于電鍍鉻鍍層。目前航空航天等領(lǐng)域中一部分原本采用電鍍鉻進(jìn)行表面處理的超高強(qiáng)鋼零件已更改為高速火焰噴涂工藝,從而實(shí)現(xiàn)對(duì)零件更好的防護(hù)。
另一方面,學(xué)者們開展了在超高強(qiáng)度鋼表面以不同類型噴涂材料或噴涂工藝制備涂層性能的對(duì)比研究,以獲得實(shí)際使用狀況下優(yōu)選的高速火焰噴涂材料或工藝。郭智興等對(duì)比研究了300M鋼表面WC-17Co、WC-10Co-4Cr、Cr3C2-25NiCr三種涂層的性能。WC-17Co涂層的致密度最高,WC-17Co、WC-10Co-4Cr涂層的平均顯微維氏硬度接近,約為1190 HV,Cr3C2-25NiCr硬度約940 HV,Cr3C2-25NiCr的摩擦系數(shù)更低。Voorwald等對(duì)比研究了以AISI 4340鋼為基體的WC–17Co與WC-10Co-4Cr涂層試樣的軸向疲勞與耐鹽霧腐蝕性能。WC-10Co-4Cr涂層試樣具有更高的軸向疲勞強(qiáng)度與更好的耐鹽霧腐蝕性能。Souza等以AISI 4340鋼為基體制備了Cr3C2–25NiCr與WC-10Ni涂層試樣。Cr3C2–25NiCr涂層試樣的耐鹽霧腐蝕性能更為優(yōu)異,WC-10Ni涂層具有更高的疲勞強(qiáng)度,相比于基體試樣疲勞強(qiáng)度基本無下降。
周克崧等采用HVAF工藝以300M鋼為基體制備了WC-17Co和WC-10Co-4Cr涂層試樣。軸向疲勞結(jié)果顯示兩種涂層試樣的疲勞強(qiáng)度接近,且略高于300M鋼試樣。鹽霧腐蝕結(jié)果顯示W(wǎng)C-10Co-4Cr涂層試樣性能更為優(yōu)異,涂層經(jīng)400 h鹽霧腐蝕后WC-17Co涂層試樣的基體已經(jīng)發(fā)生腐蝕,而WC-10Co-4Cr涂層試樣中,由于Cr能優(yōu)先在表面形成較為致密的氧化鉻膜,抑制粘接劑材料的溶解,阻礙腐蝕介質(zhì)擴(kuò)散到界面,提高涂層的耐腐蝕性能,基體未見腐蝕跡象。
Liu等對(duì)比研究了以300M鋼為基體分別采用HVAF工藝與HVOF工藝制備的WC-10Co-4Cr涂層試樣的性能。使用空氣可以降低焰流溫度,HVAF工藝下涂層脫碳較少,高溫形成W2C相含量較低,HVAF工藝制備涂層具備更低的孔隙率(0.74%)、更高的顯微硬度(1162 HV0.3)、更高的結(jié)合強(qiáng)度(74.68 MPa)及更優(yōu)異的耐磨性和耐腐蝕性。HVOF工藝中粒子速度和溫度值分別約為500~800 m/s和3000 ℃,而HVAF的飛行粒子速度和溫度分別約為700~1200 m/s和1800 ℃,相對(duì)較低的粒子溫度和較高的粒子飛行速度使得HVAF工藝下粉末的氧化和熱影響顯著減少,且易獲得孔隙率較低、與基底結(jié)合強(qiáng)度較高的涂層。高速火焰噴涂工藝目前已逐步替換電鍍鉻工藝對(duì)超高強(qiáng)度鋼進(jìn)行防護(hù),發(fā)展高致密、高結(jié)合力、高耐磨、高耐蝕、高疲勞性能的涂層是當(dāng)前主流研究方向。
2.2 冷噴涂
冷噴涂技術(shù)于20世紀(jì)80年代由俄羅斯理論與應(yīng)用力學(xué)研究所發(fā)明,并在20世紀(jì)90年代末開始商業(yè)化應(yīng)用,其原理為當(dāng)粒子撞擊速度超過某個(gè)臨界值,來自粒子-基底的撞擊能量會(huì)引起粒子強(qiáng)烈的塑性變形,在某些情況下,還會(huì)引起基底表面的塑性變形。這一過程打破了基底和顆粒表面的薄膜,在基底和顆粒之間建立了緊密的接觸,從而形成了牢固的結(jié)合。冷噴涂工藝具有低的焰流溫度與高的粒子速度,使該工藝具有涂層孔隙率低、粉末不易氧化和相變、沉積率高、基體材料受到的熱影響小等優(yōu)點(diǎn)。采用冷噴涂工藝對(duì)超高強(qiáng)度鋼進(jìn)行表面防護(hù),主要的研究方向?yàn)閷?duì)電鍍鎘工藝的替代研究,相關(guān)研究?jī)?nèi)容側(cè)重于耐腐蝕性能的研究。
石仲川等采用冷噴涂技術(shù)在300M鋼表面制備了鋁鋅復(fù)合涂層,該涂層較為致密,中性鹽霧試驗(yàn)條件下防護(hù)性良好,即使涂層損傷在770 h后才出現(xiàn)明顯腐蝕;戶外大氣環(huán)境下涂層試樣12月后表面外觀依然良好,且涂層試樣的軸向疲勞結(jié)果與300M鋼試樣基本一致。該團(tuán)隊(duì)還在300M鋼表面制備了鋅-15%鎳復(fù)合涂層,中性鹽霧試驗(yàn)條件下涂層破損試樣在660 h后才出現(xiàn)腐蝕;戶外大氣環(huán)境下涂層試樣12月后未出現(xiàn)明顯腐蝕,該涂層試樣軸向疲勞試樣基本等同于300M鋼試樣。
采用冷噴涂技術(shù)對(duì)超高強(qiáng)度鋼進(jìn)行防護(hù)尚處于研究階段,一方面是由于適用于該技術(shù)的成熟粉末材料種類相對(duì)較少,現(xiàn)階段僅鋁、鋅、銅等易變形材料形成工業(yè)化制備能力;另一方面防護(hù)層的性能是需要綜合考慮的,需要進(jìn)行大量的試驗(yàn)驗(yàn)證工作。冷噴涂工藝對(duì)基體無熱影響且產(chǎn)生壓應(yīng)力的優(yōu)勢(shì)十分突出,可認(rèn)為是極具潛力的超高強(qiáng)度鋼防護(hù)工藝。
三、結(jié)語
超高強(qiáng)度鋼材料以其優(yōu)異的力學(xué)性能廣泛應(yīng)用于航空航天、艦船等領(lǐng)域的關(guān)鍵承力部件中,嚴(yán)苛的使用環(huán)境使其在未進(jìn)行表面防護(hù)處理的情況下較快失效,因此必須進(jìn)行有效的防護(hù)處理。目前對(duì)于超高強(qiáng)度鋼材料已經(jīng)工業(yè)化應(yīng)用或極具應(yīng)用潛力的表面涂(鍍)層防護(hù)處理工藝,包括電鍍鉻、電鍍鉻、高速火焰噴涂、冷噴涂,在上文中已經(jīng)進(jìn)行了較為詳細(xì)的介紹。
總的來看,從環(huán)保角度出發(fā),噴涂工藝相較污染性更大的電鍍工藝更有發(fā)展前景。從對(duì)基體材料的性能影響來看,噴涂工藝不存在氫脆的風(fēng)險(xiǎn),涂層較為致密無裂紋,基體內(nèi)應(yīng)力以壓應(yīng)力為主,相比于電鍍工藝對(duì)于基體材料性能的負(fù)面影響較小且高速火焰噴涂工藝中的高速空氣燃料火焰噴涂工藝、冷噴涂工藝,相較其他噴涂工藝對(duì)基體材料的損傷或影響程度更小。
鑒于防護(hù)層需要考慮耐磨、耐腐蝕、界面結(jié)合力、內(nèi)應(yīng)力、氫脆、疲勞、表面粗糙度、可加工性能、可修復(fù)性能等多種性能,因此工程技術(shù)人員應(yīng)根據(jù)實(shí)際情況選用合理表面防護(hù)工藝。未來防護(hù)層的發(fā)展趨勢(shì)包括:綠色環(huán)?;?、低成本化、高性能化。且噴丸、涂漆、超聲波振動(dòng)、激光等多種工藝也將助力涂(鍍)層防護(hù)處理工藝。
四、夢(mèng)能服務(wù)與支持
1、免費(fèi)樣品
如果您對(duì)我公司的工業(yè)重防腐油漆產(chǎn)品有需要或者申請(qǐng)樣品試用,請(qǐng)與我們的客服人員取得聯(lián)系。400-878-0506
油漆樣品適用范圍:
用于新建項(xiàng)目:驗(yàn)證油漆配套的可行性、檢驗(yàn)附著力、效果圖與實(shí)際顏色的色差。
用于維修項(xiàng)目:驗(yàn)證與舊涂層的兼容性。
用于日常修補(bǔ):提供少量樣品用于修補(bǔ)破損處。
申請(qǐng)用量:在1KG以內(nèi)免費(fèi)送貨上門。
2、免費(fèi)打樣
如果您想看到工業(yè)重防腐油漆在產(chǎn)品上的實(shí)際應(yīng)用、外觀、性能測(cè)試,請(qǐng)與我們客服人員聯(lián)系,將樣板寄往夢(mèng)能科技營(yíng)銷部,由專業(yè)噴涂人員為樣板提供油漆打樣。
3、服務(wù)團(tuán)隊(duì)
夢(mèng)能對(duì)技術(shù)服務(wù)團(tuán)隊(duì)始終進(jìn)行一系列的標(biāo)準(zhǔn)化管理,從專業(yè)培訓(xùn)到日常報(bào)告的管理都有一整套完善的體系。夢(mèng)能公司每年都會(huì)對(duì)技術(shù)服務(wù)人員進(jìn)行定期的技術(shù)培訓(xùn)和能力審計(jì),以使每一位技術(shù)服務(wù)人員保持高水準(zhǔn)的專業(yè)素質(zhì),每一位技術(shù)服務(wù)人員都配備先進(jìn)的涂裝檢驗(yàn)儀器,儀器設(shè)備均按規(guī)定的時(shí)間期限進(jìn)行定期校驗(yàn),以保證每套儀器設(shè)備工作狀況良好。
4、購(gòu)買通道
零售:購(gòu)買50kg以內(nèi),線上購(gòu)買,抖店直接下單購(gòu)買。
工廠業(yè)務(wù):長(zhǎng)期合作、量大從優(yōu)、生產(chǎn)調(diào)試、質(zhì)量檢測(cè)、開具13%專用發(fā)票
貿(mào)易、代理:提供代工業(yè)務(wù)支持,項(xiàng)目保護(hù)。
業(yè)主、總包、設(shè)計(jì)院:提供防腐方案設(shè)計(jì)、性能檢測(cè)、施工方案、現(xiàn)場(chǎng)技術(shù)指導(dǎo)。
涂裝施工:提供解決方案、現(xiàn)場(chǎng)技術(shù)指導(dǎo)。
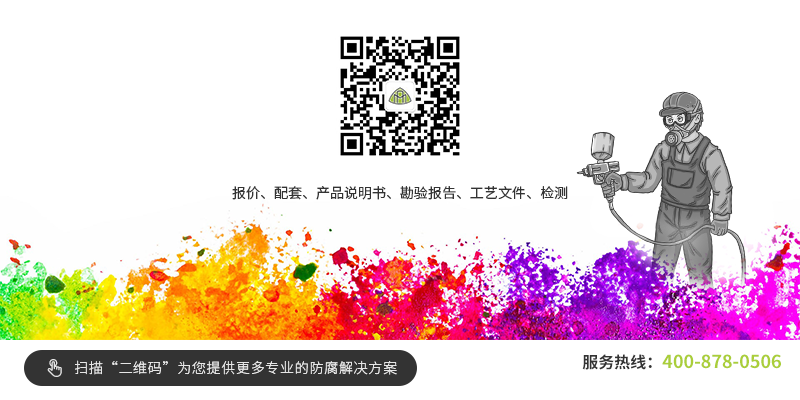